{{serverconnectlatestnews.data.showlatestnews.data[0].news_title}}
{{serverconnectlatestnews.data.showlatestnews.data[0].news_date.formatDate("d MMM yyyy")}}
{{serverconnectlatestnews.data.showlatestnews.data[0].news_teaser}}
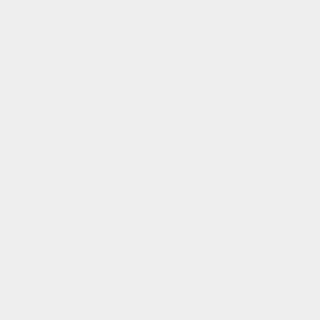
Embedded real-time analysis of continuous casting for machine-supported quality optimisation.
The project has received funding from the Research Fund for Coal and Steel under grant agreement No. 847334.
The thermal and fluid-mechanical conditions in continuous casting moulds are not precisely known although highly relevant for the product quality. Manual process control is very difficult due to the large number of influencing factors which are often happening time-shifted. The aims of the project are the optimised control and digitalisation of continuous casting machines aiming at an optimised product quality. Large data streams from different sources and of different types will be brought together and analysed online in a Big Data environment. Assistance for the caster operators will be given by real-time support system. This will provide suggestions for adjusted casting conditions in real-time. Additionally, predictions of the probability of defects will be estimated based on the current caster status and an intensified product inspection will be suggested if necessary.
These project aims will be supplemented by new measurement technologies for thermal and caster powder monitoring. Defect promoting scenarios will be identified by application of statistical data analytics and correlations with quality data of the heavy plates and cold-rolled strips. These scenarios will be represented with a digital twin of the continuous casting machine aiming at identification of thermal and fluid-mechanical reasons for the observed defects. The digital twin also allows the development of countermeasures aiming at the avoidance of casting defects that can lead to decreasing rolled product quality.
The work will lead to rules and guidelines which will be checked in real-time assessing the current status of the casting machine. The findings from the statistical data analytics as well as the developed countermeasures will be the basis for the rules and guidelines aiming at an optimised process control. Both will be integrated in the real-time support system and applied online. The effectiveness of this approach will finally be verified in industrial trials.
Dates - 1st July 2019 – 31st December 2022
Sponsor - EU Research Fund for Coal and Steel (RFCS)
EU Contribution - €1,260,471
Overall Budget - €2,100,785
BFI (Germany) – Coordinator
Materials Processing Institute (United Kingdom)
AG der Dillinger Huettenwerke (Germany)
Centre de Recherches Métallurgiques asbl (CRM Group) (Belgium)
Voestalpine Stahl GmbH (Austria)
Minkon SP ZOO (Poland)