{{serverconnectlatestnews.data.showlatestnews.data[0].news_title}}
{{serverconnectlatestnews.data.showlatestnews.data[0].news_date.formatDate("d MMM yyyy")}}
{{serverconnectlatestnews.data.showlatestnews.data[0].news_teaser}}
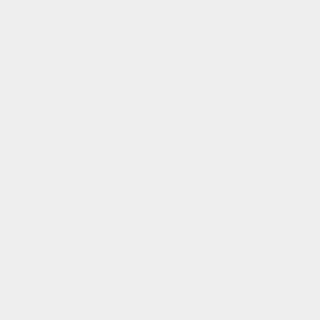
A bespoke specialist melting and casting service:
The Materials Processing Institute offers a range of steel alloys and revert melting services on a commercial basis. Product is available as ingots up to 6 tonnes, including for specialist applications in sectors such as: nuclear, defence, offshore, aerospace and engineering.
The main area of expertise is in melting, alloying and casting of semi-finished product, produced at the Institute's production facility in Middlesbrough, UK. A complete service can be offered, including downstream processing.
Steel alloys are manufacturing to customer specifications, within short lead times and with a high degree of cleanness, using vacuum degassing and argon purging.
Available as:
Smaller batch and cast sizes are also available on request, particularly suitable for revert melting.
Revert melting allows the recovery of valuable by-products. The resulting scrap and processing materials can be re-melted into a custom form of size, shape and weight, suitable to be re-used as a raw material according to client requirements.
An increasingly popular service for scrap suppliers and steel and metal processors, assay melting allows for accurate and independent analysis of as supplied scrap. This is essential for both optimum process control and to assure the agreed specification of scrap supplied under a commercial contract. The ability to melt a 6 tonne charge ensures that a truly representative sample of the scrap can be achieved and independently verified.
The Institute has supplied to a wide range of clients and markets, including forging operations, rolling mills, stockholders, supply chain management companies, engineering companies, steel manufacturers, rod and bar drawers, wire manufacturers, extrusion companies and recycling operations.
Geographical markets include the UK and more widely in Europe and end use applications include: nuclear, defence engineering, aerospace and marine.
The Institute is accredited to ISO 9001:2015 and ISO 14001:2015.
The Materials Processing Institute uses advanced steel processing technology and facilities to produce bespoke steel alloys, in cast sizes up to 6 tonnes. A range of smaller furnaces are also operated for specialist applications and sand casting facilities are available, particularly suitable for revert melting.
The primary melting facility is an electric arc furnace. Secondary steelmaking facilities include ladle furnace and vacuum tank degassing, enabling a wide range of steels to be produced from conventional carbon/manganese grades, through to and including some complex, multi-alloy stainless steels.
Process control is achieved through sample analysis and optical emission spectroscopy, to continually update the alloy composition in the melt. The facility is supported by a suite of analytical laboratories for both metals and slags, including scanning electron microscopy.
Ingots are bottom filled using a trumpet and runner arrangement and can be purged and shrouded with inert gas.
The commercial manufacture of steel alloys at the Materials Processing Institute, draws on decades of expertise in developing new and unconventional steel alloys for sectors including: rail, defence and automotive. The steel processing expertise of the wider Institute includes sophisticated modelling, measurement and control technologies.