{{serverconnectlatestnews.data.showlatestnews.data[0].news_title}}
{{serverconnectlatestnews.data.showlatestnews.data[0].news_date.formatDate("d MMM yyyy")}}
{{serverconnectlatestnews.data.showlatestnews.data[0].news_teaser}}
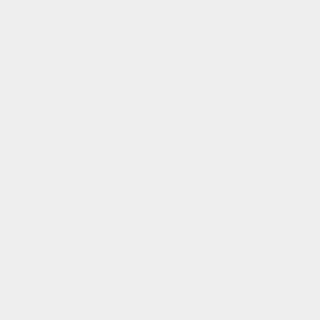
Recycled concrete fines, a low-carbon cement substitute to accelerate decarbonisation of the concrete industry.
The Recycled Concrete Fines project has received funding from UKRI as part of the Contracts for Innovation: Decarbonising Concrete competition.
The UK construction industry needs to find alternative materials to slag and fly ash, which are scarce, but needed to decarbonise concrete. This project seeks to offer an alternative, using recycled concrete fines (RCF). The innovation in this project is the development of new cement and concrete formulations using RCF. It aims to decarbonise concrete by replacing Portland Cement with RCF produced from waste.
A widely adopted practice to lower carbon emissions from concrete is minimising Portland cement use by partially replacing it with other materials. Slag and fly ash are the most used types, but their availability is either very limited in the UK or they are fully utilised. To fill the gap in the slag or fly ash supply, the industry is looking to replace Portland cement, not only with these materials, but also with limestone. However, this solution is only temporary, as slag and fly ash will become scarcer. Other solutions currently being explored include calcined clay, but too much reliance on clays will hinder resource efficiency. An alternative approach is to treat RCF and use them as slag or fly ash substitute.
An alternative approach is to treat recycled concrete fines (RCF) and use them as slag or fly ash substitute.
RCF typically constitutes about 15% of the total recycled concrete. In the UK, the coarse fraction of recycled concrete is commonly used as a substitute for natural aggregates in some applications, while the fines are downcycled or landfilled. Recent advancements have made it possible to separate the fines from the coarse fraction, especially the hydrated cement fraction, and use them for other purposes, including partial Portland cement replacement.
Using RCF as Portland cement substitute is not considered by the UK concrete standards (BS 8500), partly due to its low reactivity. However, there are ways to improve RFC reactivity. Improved reactivity is anticipated to enable about 50% Portland cement substitution, a level comparable to what is typically achieved with slag.
The aim of this project is twofold. First, it will address the RCF reactivity. To do this, RCF will be either carbonated or calcined. Second, concretes made with a range of cement compositions based on RCF will be rigorously tested against the current EU/UK standards. This is to revise BS 8500 to allow for high Portland Cement substitution with RCF.
Revising BS 8500 will remove barriers to the wider adoption of RCF in the UK market. As a result, this project will enhance UK supply chains by providing alternatives to slag and fly ash for the concrete industry, addressing waste management and circularity challenges in the concrete industry. The construction industry has shown interest in using RCF as soon as BS 8500 permits.
It is also hoped that the methodologies developed and used in this project will provide a development template which can be applied to examine any other potential substitute materials for Portland cement.
In addition to reducing waste and improving circularity, this project will enhance UK supply chains by providing new lower carbon resource efficient products for the construction industry.
Dates - September 2024 – September 2025
Sponsor - Innovate UK
Project Value - £449,231
Materials Processing Institute - Lead Partner
Subcontractors