{{serverconnectlatestnews.data.showlatestnews.data[0].news_title}}
{{serverconnectlatestnews.data.showlatestnews.data[0].news_date.formatDate("d MMM yyyy")}}
{{serverconnectlatestnews.data.showlatestnews.data[0].news_teaser}}
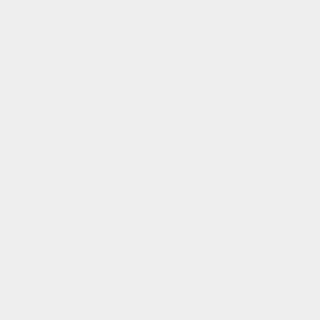
The Materials Processing Institute, British Steel, Wienerberger UK Low Carbon Europe and Heatcatcher Ltd have collaborated in this UK steel and ceramics sectors Industrial Strategy Challenge Fund (ISCF) project to share best practice and investigate waste heat recovery from furnaces.
Furnaces used in both industries are gas fired and operate continuously heating products to temperatures over 1000°C.
Both industries currently use waste process heat to good effect and use exhaust heat to pre-heat product. The brick kiln using further exhaust heat for drying products and the steel furnace recuperating heat into combustion air. The steel furnace also uses its cooling system to generate steam for other uses on the steel plant.
The project compared a reheating furnace operated by British Steel, with brick kilns operated by Wienerberger UK; investigating combustion efficiency and heat flows to assess contrasting practices and heat use in the processes.
The project identified opportunities to:
Benefits identified included:
The findings of this project highlighted how these highly efficient processes might further improve and become less carbon intensive using improved heat recovery and combustion technologies. These improvements will typically be possible on all similar continuous reheating furnaces and brick kilns.
Enquire about services, facilities, and expertise.