{{serverconnectlatestnews.data.showlatestnews.data[0].news_title}}
{{serverconnectlatestnews.data.showlatestnews.data[0].news_date.formatDate("d MMM yyyy")}}
{{serverconnectlatestnews.data.showlatestnews.data[0].news_teaser}}
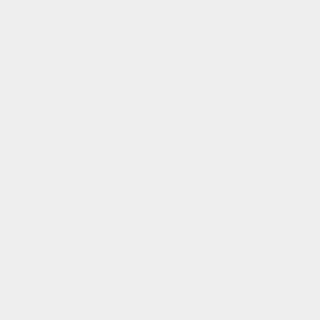
Heat distribution curve across furnace
Particle flow velocity profiles
Simple furnace model mesh
The Materials Processing Institute has developed a Computational Fluid Dynamics (CFD) model for hydrogen combustion in industrial heating furnaces, a vital new tool to assist clients in assessing and modelling the changes in heat distribution and transfer, exhaust gases and product heat profiles that occur with a transition from natural gas towards hydrogen, and from air to oxygen. Complementing this model in the coming year will be hydrogen fuelled reheating facilities using modified commercial burners to enable physical product and equipment investigations.
Furnaces used in industry regularly heat metal products up to 1250°C, often using natural gas as a fuel. Nationally, trials have been carried out to ascertain how the main gas network and end users will adapt to blending up to 20% hydrogen into the network supplies, recognised as staying with in the limits of most standard equipment and operations. But the future will require much deeper decarbonisation of heating, and one major option for high temperature process industries will be transitioning to pure hydrogen combustion.
To establish how furnaces in industry will operate under hydrogen as a fuel, a 3D model and CFD model are being used to evaluate the changes in performance of commercial heat treatment or melting furnaces in the 900-1250°C category under different gas regimes, starting with steel reheat furnaces.
The model compares the operations of furnaces operating on a range of gases or liquids in the burners and how increased percentages of hydrogen (up to 100%) into the fuel mix will affect the operation.
Additionally, the model can be used to predict the emissions given off through the process, of particular importance is the change in NOX emissions, which can be forecast using the model.
The structured workshops identified the stakeholders, project success factors, project value drivers and potential Industry 4.0 ideas, resulting in a value chain map of ideas and a prioritisation chart based on benefits and ease of implementation.
Hydrogen as a fuel reacts very differently to other fuels – from an operational point of view, flame speeds and temperatures are higher than standard natural gas. This model will:
The use of CFD as part of the solution to establishing how fuel switching will affect operations will help the Institute to guide industry into decarbonisation. The decarbonisation using this method can be applied to all furnace types and preheating systems.
Enquire about services, facilities, and expertise.