{{serverconnectlatestnews.data.showlatestnews.data[0].news_title}}
{{serverconnectlatestnews.data.showlatestnews.data[0].news_date.formatDate("d MMM yyyy")}}
{{serverconnectlatestnews.data.showlatestnews.data[0].news_teaser}}
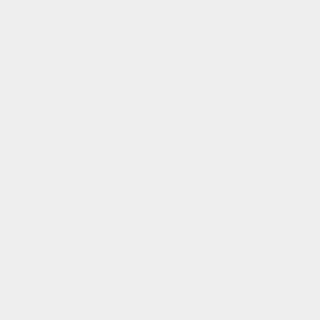
This course gives and introduction to the topics of refractories, their properties and role in the steel industry (insulation, containment, safety, quality control…) and the mechanisms of wear and degradation.
In the later parts of the course we look at the specific refractories and needs in particular parts of the steelmaking and casting process ranging from the primary steelmaking vessels (BOF or EAF) to the ladle, tundish and casting refractories. This looks at the types of refractories used for different applications, their care and maintenance.
On demand and instant access to the full course consisting of three modules.
To maximise learning it is recommended that each module is completed in sequence.
The full course consists of three modules which should be taken in sequence in order to complete the full course.
This module covers what a refractory material is and the different types of refractories (acid, neutral and basic materials, bricks, hollow-ware, castable refractories, cements, rammed and sintered materials). Selection of different materials for different applications and how refractory cost varies through the process route are considered. The different influences on refractory wear (erosion, corrosion, thermal and mechanical shock…) and the role of carbon are introduced. The operational considerations to manage refractory performance such as drying, curing, preheat and thermal cycles as well as stable operating conditions are noted.
Module 2 builds upon the principles discussed in Module 1 and considers the refractories used in primary steelmaking processes in the Basic Oxygen Steelmaking Furnace (BOF) and the Electric Arc Furnace (EAF). The module introduces the different types of refractory used in different parts of the furnace and the reasons for these choices. The need to protect, replace or repair refractory in areas of high wear are noted and the effect of progressive wear and repair on furnace operational costs and in determining the optimal timing of reline.
Module 3 discusses refractory types and requirements in the secondary steelmaking, refining and continuous casting process (ladle, tundish and continuous casting). The purpose of different refractories in different parts of the process and operation are introduced. The importance of control of thermal cycles (correct preheat and control operating cycle) as well as control of flow and temperature for metal and slag to ensure both good product quality and optimum refractory performance are noted. Examples are given of refractory failure and wear and how design and operation aim to avoid this.
The course gives a comprehensive introduction to the importance of refractories and the principles behind the correct choice and use of refractories in a steelmaking and casting environment.
The course is appropriate for steel plant operational, engineering and technical support teams in the early stages of their career, or for more experienced personnel moving into a new role in a steelmaking and casting environment.
For those requiring a higher level of expertise, theoretical or practical detail, additional information and advice is available from enquiries@mpiuk.com.
3 x 40 minute modules
Alan Scholes
Chief Technology Officer
Materials Processing Institute
Over 30 years experience in steelmaking and casting developments.
Awarded IOM3 (Institute of Materials, Minerals & Mining) Gilchrist-Thomas Medal for developments in secondary steelmaking.
Alan Scholes has had a career in process R&D, focussed mainly in liquid steelmaking, secondary refining and continuous casting. This has involved scale-up and implementation of processes on many production plants in the UK and Europe including several large multi-national projects as both partner or leader. Practical knowledge of both the process and its effect on production (such as refractories) is essential. In addition, Alan had experience of managing and upgrading the Materials Processing Institute’s 7t pilot scale steelmaking facility where refractories are called upon to endure a wider range of operating extremes than for routine production. He has been a technical expert evaluator for R&D projects, proposals and papers for both UK and European publications, conferences and funding bodies.
Enrol for the full course, or go through the modules separately (to maximise learning it is recommended that each module is completed in sequence).
Full Course
(save $40)
$185.00
Module 1
Principles and considerations
$75.00
Module 2
Refractories for steelmaking processes
$75.00
Module 3
Ladle, tundish and casting refractories
$75.00
$40.00 discount available when you purchase the three modules together.